Posts
Showing posts from 2019
PULP contemporary research
- Get link
- Other Apps
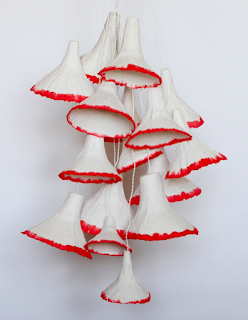
https://www.upcyclist.co.uk/2017/02/10-eco-chic-lighting/ https://www.upcyclist.co.uk/2016/01/vessels-made-from-paper-pulp-by-debbie-wijskamp/ https://www.eternitystew.com/Formulations https://www.eternitystew.com/Paper-Islands Sculptures are made with paper fiber and plaster or paper pulp; acrylic paint, cut painted paper, metal leaf, and pigmented concrete.
PULP structures
- Get link
- Other Apps

PULP structures made using flat sheets of partially dry paper dyed with blue ink. The two images below were made using a semi dry piece of paper. I moulded the paper on the insisde of a bowl. This created cracks in the bottom of the bowl as i had to push it in to form the shape. For the next pot, I draped the paper over a jar and created folds to both mould it and create some texture. Although i'm pleased with the stability of this piece i think the folds make the piece look too messy and not the look i'd like to achieve. This was the most successful of the tests as the shape is really strong and can actually be used to store pens etc. as it holds itself up well. I also really like the texture that has been pressed into the paper from the tea towel it was placed on to dry. I want to try imprinting various other patterns into the paper to give them a more interesting, decorative look and to maybe make them look less like paper. Research for my CP3 ess
PULP development 2
- Get link
- Other Apps
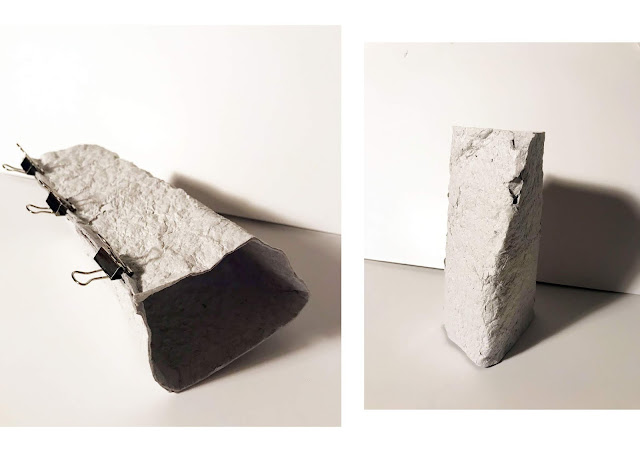
After producing a flat piece of paper, as shown in previous post, i left it to dry completely. This took about 5 days. I then tried to shape it just creating folds to test how well it could be moulded. The video above shows a piece that had come apart from the large piece due to the paper being made up of six small pieces. I found the paper too brittle to bend into a nice curve and the more i played around with it the more it cracked and began to fall apart. I then used the bigger piece and tried to bend it on a straight line as oppose to a curve. This worked slightly better but still created cracks. After i had folded it i decided to spray it lightly with water to soften the corners. This allowed me to create softer corner and to push the cracks back together. Currently, the open seam is held together by bulldog clips. I have wet the edges and i'm hoping that they'll start to fuse together. I don't think this method works as i'd like it to as i can
PULP Development
- Get link
- Other Apps
7th October PULP development Evident in the previous blog post, my pulp pieces have not been very successful thus far. I decided to proceed with the project i needed to switch up the method drastically, my main problem before was the removal of the pieces from their mould. My plan to eliminate that problem is to make flat pieces of paper pulp and mould them once they are dry/partially dry. This stage of the experimentation will focus mainly on drying time and thickness of the paper. The videos above show the process of making flat sheets of paper using a frame and deckle and pulp. Since my frame is so small i am attaching 6 pieces together to allow me to create larger pieces. The problem with pushing them together is that you end up with weak points in the paper so i will try and craft a larger frame using a photo frame and some fine mesh of some sorts. I'm going to leave this piece to fully dry and then mould it into a shape. In the meantime i will continu
PULP
- Get link
- Other Apps

23rd September PULP AIM - use recycled paper waste to create pots, vases and bowls that can be used in a variety of ways (both functional and decorative) How will i find the best method? test different types of paper different ways of moulding the vessels different ways of adding colour different soaking times/amount of water length of drying time before de-moulding adding in other materials? thickness of paper - how does it affect stability/ability to dry fully First test -Using waxy papers and crushed broken old paper bowls and tissue. -Using a mix of fibres to see if that allows the pulp to hold together better. -Left to soak for a couple of hours then blended with a lot of water -Applied to mould still quite wet and applied in a medium thickness. Thickness worked well/held together relatively well but the removal from the mould is what cracked the edges - need to find a better way of doing that. Maybe grease mould/add a laye
Evaluation – Self Initiated
- Get link
- Other Apps
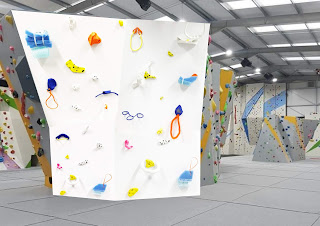
In my self-initiated project, I aimed to push myself to work with materials I don’t regularly work with as I have found in previous projects it is easy to allow yourself to become comfortable with materials. So, after deciding in wanted to focus on rock climbing walls, and the feeling of climbing as my theme I began making 3D samples, using different materials with 3D capabilities such as clay, sponge and fabrics filled with rice/wadding. Visually, I found my samples really interesting but felt the initial ideas I wanted to portray had been lost through my making process. This is when I started adding more interactive components into my samples. This is also when the idea came to build a non-functioning climbing wall. Something that would appear to support you but in actual fact would cause you to fall, emulating the feeling I have when rock climbing. For example, below is a sample made from Baked clay and para cord, seemingly strong but when weight was ap
Engineering Embroidery Visualisations
- Get link
- Other Apps
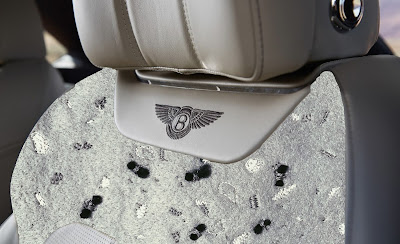
Below are visualisations of how my samples could be used in place of traditional interior materials to add elements of texture and softness, in the examples below, to the seats and car door panels. I think this sample works particularly well when situated in the context of a luxury car as the colours match the subtlety of those used in the Bentley shown below.
Engineering embroidery - Evaluation
- Get link
- Other Apps
I began this project by thinking about how I could challenge both myself, and the brief. My initial thoughts were to look at different elements luxury cars possess, such as seatbelts, seat covers, dashboards etc. and how I could reinvent these elements in a more exciting fashion. However, after beginning my research I became interested in the idea of making Luxury more familiar. This idea stemmed from travelling on the London Underground, noticing the interior, specifically the tube flooring. I wanted to incorporate the speckled pattern of the flooring and the colour scheme into the more traditional interiors of luxury cars. As noted on the brief, “Rolls-Royce cars have developed the finest quality ‘embroidered’ high-end bespoke car interiors” so I decided to set myself the constraint of working exclusively in machine/hand embroidery during this project. I wanted to ensure I maintained a level of attention to detail within my work as well keeping elements o